Many owners wonder if they should use modular construction. Will it save both money and time, without sacrificing quality? Will they get what they want with modular or do they have to make sacrifices? This article attempts to bring clarity to those questions.
As you may have expected, there is a clear relationship between savings with modular and the complexity of the design. This is true of all construction but has an exponential effect with modular. This is because modular manufacturers produce modules as predesigned and pre-engineered elements. The extent of adjustment or changeability to these elements will change the cost.

To make this point, consider common examples of the least changeable modular systems: tents, sheds, industrial high bay enclosures, and portable classrooms. In each case, the owner values quality space but does not need to change or modify the system in order to maximize value.
There are many examples of non-custom, “off-the-shelf” modular systems that provide a multitude of owners exactly what they need without design modification. An automobile is also a good example of such a system. Many people choose to buy Ford, 150’s, 250’s, and 350’s, they accept the system and value the result.
However, as we know buildings are more complicated. In many cases, the needs of building owners are such that the introduction of significant limitations on customization will not meet their needs. That is why for years many modular manufacturers fully adapt to custom designs. Some modular manufacturers build “in place” for a singular owner and do not use an assembly line process. They are simply building a custom building in a conventional manner but away from the site.
In this environment, they may not be fully leveraging repetitive design elements. The overall cost of design, related coordination, and construction costs rise to meet the same types of cost experienced with conventional buildings. If the owner’s needs, as represented by the conceptual design and complexity of systems of the building, cannot fit neatly within a modular factory “model”, it doesn’t mean that modular may not be the right choice (due to many other benefits of modular) it just means that they should not expect to save money when compared to conventional construction.
This type of approach to modular is best represented by the following Triumph case studies: MIT Koch Center, Harvard Pagliuca Life Lab, Steamship Authority, Ayer Mass DPW Office Building. All construction is inherently complex. The time savings, quality, safety, and efficiency of off-site production, and relative brevity of activity on site, are major advantages for many projects. For sake of discussion and cost comparisons see Figure 1 below: wherein we name this type of approach Fully Adaptive Modular (FAM).
It follows that Moderately Adaptive Modular (MAM) places more restrictions on the owner’s designer, forcing them to work the spaces into the factory model. This type of modular manufacturer uses pre-engineered frames, systems, and materials purchased in advance, in bulk, for more than one client’s job and an assembly line approach.
It still allows designers to manipulate the buildings in a way that makes them look unique, but to a lesser degree than the fully adaptive model. MAM produces sophisticated and stunning buildings of permanency that serve the most serious of applications. Also, the owner can and should rightfully expect cost savings when compared to traditional construction, given they have decided to adapt to the modular model.
You already knew that making alterations, or modifications, reshaping, or re-organizing a pre-engineered modular “box” would likely result in higher cost. Maybe you weren’t sure if you should go modular because of a lack of fit? Now I hope you have the answer; some projects do not save money when compared to conventional. In the worst-case scenario, you should never exceed the cost of conventional – so long as you have a good modular team.
The chart below represents 3 different general types of modular building approaches discussed above. The most expensive is represented by a proud peacock, “fully adaptive” to the deep design process delivers cost predictability, time savings, and elegance.
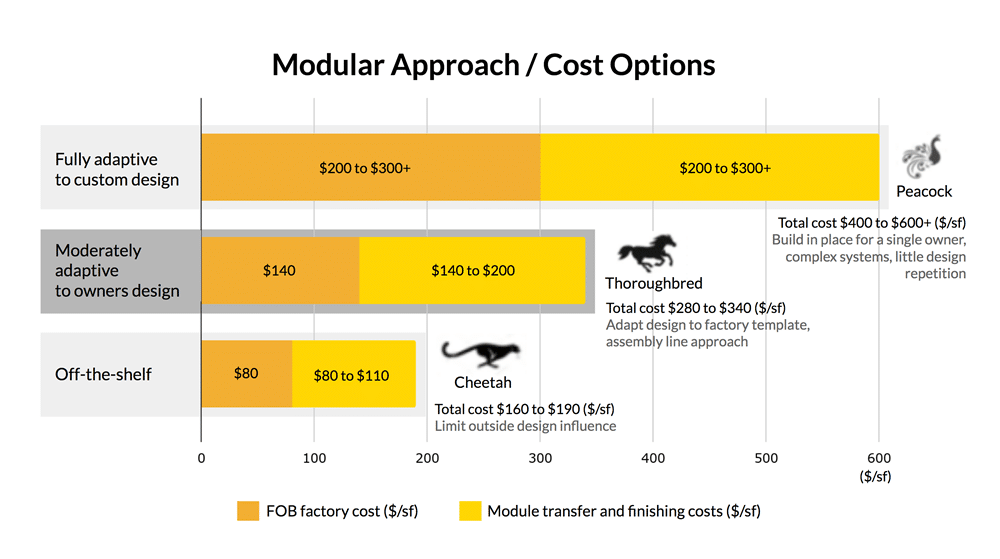
The thoroughbred defined by Websters as “truly outstanding” in the middle, may represent the most widely utilized form for modular buildings, given it arguably finds the right balance between leveraging pre-engineered elements, and adding owner’s design inspiration and custom needs. Naturally, the least expensive is where Owners seek out a predesigned and pre-engineered unit that meets their needs without extensive customization or alteration.
Each of these three types of buildings can provide great value to owners needing permanent building spaces. Where do you fall in this range? Where do you have to be? Where do you want to be? The choice is yours.