Permanent Modular Construction
Triumph Modular delivers high-performance permanent modular buildings for clients who demand speed, quality, and precision. Whether you’re planning a school, office, or institutional facility, our off-site construction approach gets your project completed faster — with less disruption and more predictability.
Modular Building Solutions, Built to Last
We specialize in custom, code-compliant modular buildings designed for long-term use. Our team manages the entire process — from design and engineering to delivery and installation — ensuring your building is on time, on budget, and built to perform.
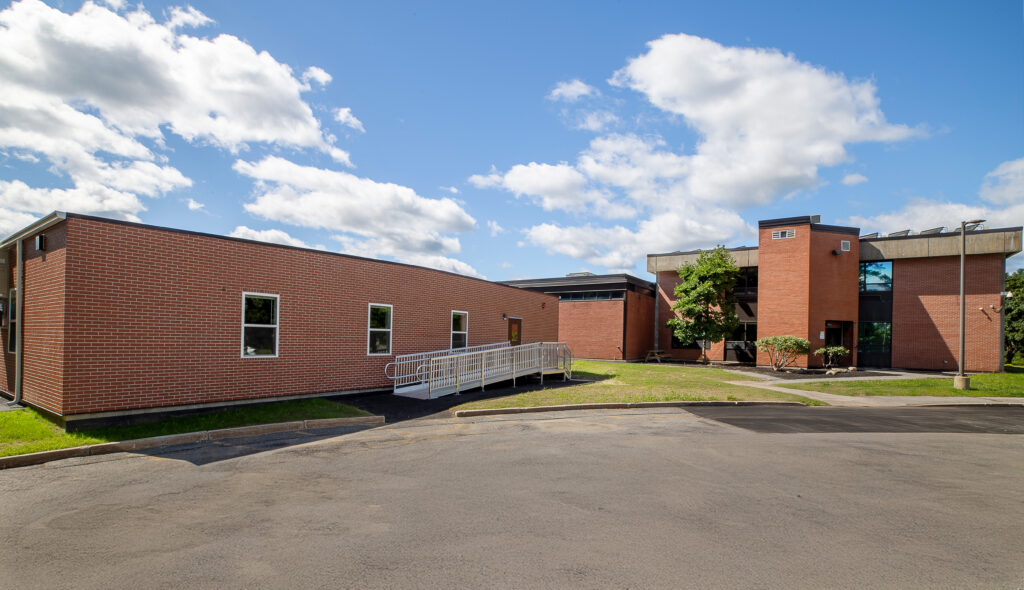
Why Choose Permanent Modular Construction?
When speed, predictability, and minimal disruption matter, permanent modular construction delivers. Triumph Modular provides durable, code-compliant buildings that rival traditional construction in both quality and design — often with significantly shorter timelines and fewer on-site challenges.
Our clients choose permanent modular solutions for:
- Fast-track school and campus expansions
- Healthcare and medical facilities with strict schedules
- Government and institutional buildings requiring rapid deployment
- Office space that needs to integrate with ongoing operations
Modular is most effective when the scope is clearly defined from the start. With fewer design changes mid-project, we can deliver faster occupancy and better cost control. If your project needs to stay on schedule, reduce site impact, and maintain high design standards, permanent modular may be your best path forward.
Permanent Modular Costs
Cost is always an important factor in purchasing decisions, and permanent modular is no exception. There are two key factors related to permanent modular construction that influence the overall cost:

Site work cost considerations can further be divided into several categories depending on the project.
These include:
Permits , lot preparation, foundation, utilities and connections, water drainage, hardscaping and landscaping.

Building cost starts with the type of building you need. Typical projects will cost less, while more complex buildings will cost more.
From there, we work through the big four:
Electrical, HVAC, plumbing and fire protection
Finally, there’s the level of finishing and materials used—both of these can add or take away from the cost, depending on what you choose.
Looking for permanent modular inspiration for your project?
Check out these examples of Triumph’s permanent modular projects and premium buildings.